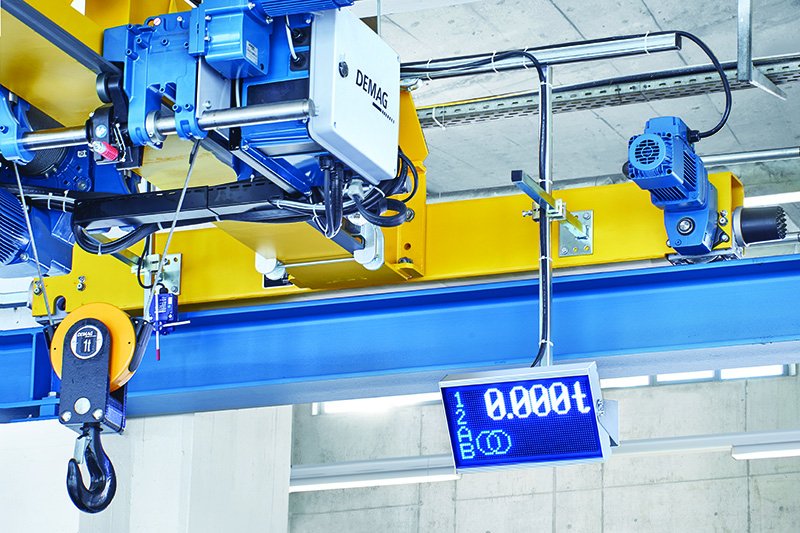
Supporting and retaining your warehouse employees may be the best way to address the labor shortage. Although technology investments tend to focus on the relentless need to increase productivity, it’s a delicate balance between employee optimization and burnout. An injury, whether isolated or cumulative, creates another unfilled position. Other workers might leave a strenuous job before it gets to that point, lured by even a relatively small paycheck bump.
In this climate, safety and ergonomic improvements are weighted much more heavily in purchasing decisions. Overhead lift assist technologies like cranes, hoists and vacuum lifters are a growing segment as employers seek to improve working conditions. Grant Welch, manager of handling systems applications engineers for Schmalz, says customer focus varies from reducing turnover to preventing injuries or speeding throughput, but one theme is consistent.
“Things are trending more toward safety than they ever used to,” Welch says. An automotive type manufacturer’s concerns and ROI calculations are different than, say, a mom-and-pop wood shop, “but I would say more and more are following the European countries in terms of being very safety conscious. For attracting and retaining employees, quality of life can be a big differentiator.”
As a result, Welch says more companies are requiring lifters for lower weights, even for 15 pounds, because lifting 2,000 units per day adds up. “They’re now looking at the total tonnage a person is handling and then building requirements around that,” he adds.
That said, new equipment or smart features are only part of the battle. From design to deployment and beyond, worker input is essential.
“We definitely run into folks who get mad at their operators for not using a tool they spent good money on, but they still have productivity rates to hit,” Welch says. “If you’re going to incentivize them to put out as much as possible, they’ll grab bags by hand if it’s faster.”
Modern reached out to several suppliers of overhead handling technologies to explore the ways the latest equipment, or upgrades to classics, are finding the sweet spot between speed and user friendliness.
Tailor the tool to the task
Customization and a growing menu of options are becoming the norm for materials handling technologies. Although they are among the simplest equipment, lift assist technologies are along for the ride. Connectivity features are increasingly standard and can be added on to existing cranes, hoists and positioners.
Customers are looking to leverage more data, or fill in data “holes,” according to Jeff McNeil, vice president of marketing and innovation for Gorbel. An expensive machine and sophisticated conveyor will collect lots of data, but if the lifting device between them isn’t smart, it’s hard to paint a complete picture of the process.
“Many end users still assume there are only two extremes: handling 80-pound bags by hand or using robots. But, there’s now a spectrum with more options in the middle,” McNeil says.
Growing companies tend to move incrementally, McNeil says, and new solutions aim to support them along the way. A machine shop might start with a prime focus on customers as opposed to efficiency, and will be drawn to multi-purpose equipment like a forklift for lifting, loading and unloading.
“When operated safely, they are wonderful, but they’re not the most efficient use of space or manpower, and not always the safest,” McNeil says. “There’s an evolution for many of our customers toward efficiency and ergonomics. As business gets better and labor or space constraints tighter, they can’t afford forklift-sized aisles in the facility and near the machines.”
Joe McCabe is the engineering manager for Columbus McKinnon’s newly formed automation division, which is developing solutions to enable customers to make gradual transitions now and going forward. He says when upgrading or designing replacement equipment on a crane, many users are now trying to make their equipment “automation-ready” for future use.
“To that end, we use diagnostic and analytics solutions that collect, organize and analyze data from measurement points throughout the equipment, from the incoming power, through the control systems and out to the driven loads,” McCabe explains.
Reports might include:
- analysis of power consumption and quality;
- variable frequency drive currents and fault histories;
- vibration and temperature feedback from drives, component enclosures, motors and bearings;
- gearbox oil viscosity;
- cycle counts of motor starts, stops and brake actuation; and
- total distance of motion.
Taken together, these data points help to build trending histories to aid in the budgeting and scheduling of preventative and predictive maintenance activities. Remote access on smart devices and PCs allows users and technicians to view equipment status in real time, or configure text and e-mail alerts about production, alarms or faults.
“In many cases, PLC hardware and network communications are an easy way to support future upgrades, but it’s important to have a plan,” McCabe says. “Users should start internal conversations early to fully understand how existing equipment is utilized and to determine the cost and benefits of each upgrade for a favorable ROI.”
Get a feel for the application
Ergonomics are the central factor driving innovation, but it goes beyond physical concerns like how workers place their hands on equipment, bend at the waist, or strain their eyes to see controls. Instead of single- or dual-speed motors, the latest hoists are often servo-based, providing a range of speeds, increased precision and reduced maintenance.
“A traditional hoist has no intelligence, so it can’t stop an operator from slamming down onto a machine,” McNeil explains. “Ergonomics might be great, but quality and cost elements are not always addressed.”
Servo control enables users to set limits depending on context. If a load is suspended over a machine, sensors will detect its position and prevent the operator from lowering beyond a certain point. These rules can even be load-specific, with one threshold for part X and another for part Y. For precision movement, the system can automatically drop to creep speed when a few inches away from its destination. McNeil describes a “float” function enabling an operator to take both hands off the controls and guide an item into position as though it were weightless.
“The idea is to use technology to simulate and amplify a worker’s ability to take uncertainty out of the process,” McNeil adds. “Technology can leverage the operator’s eyes, dexterity and intelligence without allowing them to harm themselves, machines or parts.”
Martin Marincic, director of product support for Demag, emphasizes how servos and software can keep physics from creating unwanted surprises. Anti-sway software can control acceleration and deceleration to prevent loads from swinging, no matter how fast the operator commands it to move. “You can count on an inexperienced operator to operate safely because they have that control,” Marincic says.
Connected and intelligent hardware and software also capture valuable data about the operator’s performance. Capturing is good, but McNeil says communication is even better. Recent models might require someone to plug in to extract historical data, but if reports show a unit overloaded several times in a shift, by then it’s too late to take action. To support preventative maintenance (PM) as well as unscheduled issues, real-time IoT capabilities can transmit data over Bluetooth, cell or network to maintenance personnel, managers or Cloud-based remote monitoring services.
“We do see a lot of people just running them until they break, and occasionally we get there and have to lock out poorly maintained equipment immediately,” says Marincic, who adds that smart features like tracking cycles, hour meters and average loads are only part of the solution. “By its very nature, a hoist and its components will wear, and you have to be mindful of that. It can be a chore, but in addition to replacing worn parts, we recommend a periodic overhaul, which more and more customers are embracing.”
The experts all encourage performing periodic and annual crane inspections and discourage shortcuts. Avoiding the manufacturers’ recommended maintenance intervals and procedures is a sure path to equipment failure and unplanned downtime. Customers should plan to keep spare parts on hand and be sure they are OEM parts since substitutes can undercut software’s ability to accurately calculate predictive maintenance. If available, the manufacturer or an authorized repair center should be used for all service work.
“Automotive-type operations are so used to PM schedules they follow them to a T. Those are probably the exception,” says Welch, “If you have any kind of PM schedule, tie in your lift assist equipment so you’re building off what you already have. If you know you will be changing tooling every two weeks on a CNC, take five minutes to look at a vacuum lifter and check the filter. You have to make it a habit or else you’re waiting until it fails.”
Title: Technology lifts overhead handling to new heights
Sourced From: www.mmh.com/article/technology_lifts_overhead_handling_to_new_heights#When:16:50:00Z
Published Date: 04/13/20
No comments:
Post a Comment